Future Trends in Rubber Bellow Manufacturing
- NAMRATA RUBBER PRODUCT PRIVATE LIMITED
- 12 minutes ago
- 3 min read
Rubber bellows play a crucial role in many food grade and pharmaceutical applications, providing essential functions such as vibration control, sealing, and flexibility. As they continue to evolve, so does the demand for advanced rubber bellow solutions. Manufacturers are focusing on developing new products that are more adaptable, durable, and designed for specific industrial needs.
Rubber bellows have come a long way in their evolution, adapting to changing industrial needs and technological advancements over the years. In recent years, the demand for rubber bellows in niche sectors like food processing and pharmaceuticals has reshaped production trends. These industries require products that not only meet stringent safety standards but also offer superior performance in challenging conditions.
Looking ahead, the rubber bellow industry is poised for further innovation. With the rise of automation and smart technologies. These evolving trends are shaping the future of rubber bellows, particularly in food-grade products, and what businesses can expect as they adapt to meet tomorrow's challenges.
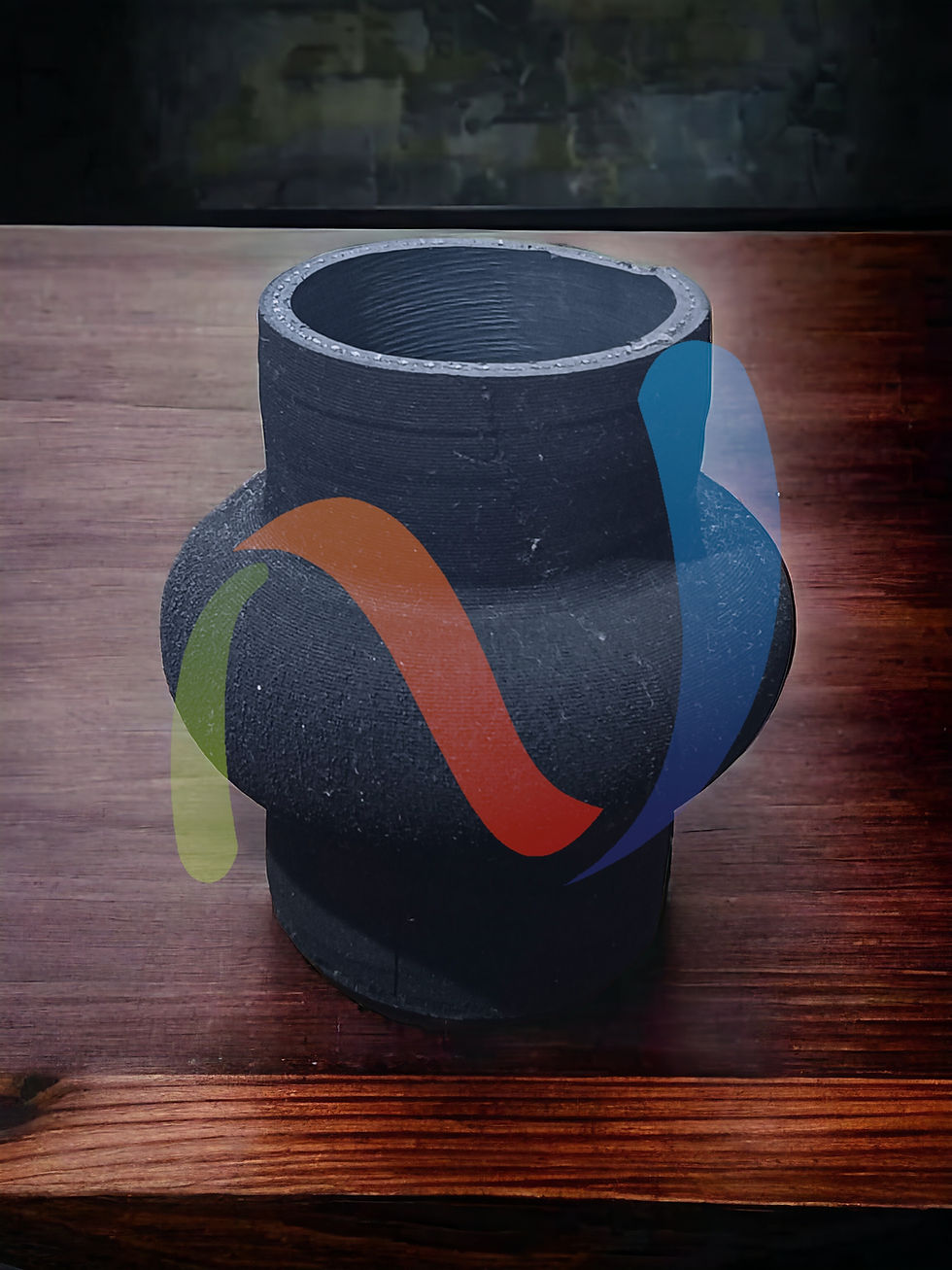
Trend 1: Customization to Meet Industry-Specific Needs
One of the most significant trends in rubber bellow manufacturing is the move towards customization. Industries are now demanding rubber bellows that are specifically designed for their unique requirements. Whether it’s for vibration control in industrial machinery or for volumetric feeders, customized solutions are becoming increasingly important.
Why Custom Rubber Bellows Are Gaining Popularity
Tailored fit: Custom designs ensure the bellows fit perfectly into machinery, improving efficiency.
Specific material needs: Custom rubber bellows can be made from materials that suit the exact requirements of the application, such as heat resistance or flexibility.
Improved performance: Tailored solutions help reduce wear and tear, leading to longer-lasting equipment and fewer maintenance needs.
Trend 2: Sustainability in Rubber Bellow Manufacturing
Sustainability is a growing priority in many industries, and rubber bellow manufacturing is no exception. Companies are increasingly adopting eco-friendly practices to reduce waste, use recyclable materials, and improve energy efficiency in their production processes.
Key Sustainable Practices in Rubber Bellow Manufacturing
Eco-friendly materials: Manufacturers are using recyclable and biodegradable materials in the production of rubber bellows.
Energy-efficient production: The industry is focusing on reducing energy consumption during manufacturing.
Waste reduction: Many companies are working to reduce material waste through more efficient manufacturing processes.
Trend 3: Advancements in Material Technology
Material technology is playing a pivotal role in the evolution of rubber bellows. New materials are being developed to meet the demanding needs of modern industries. Whether it’s silicone rubber bellows for high-temperature applications or food-grade rubber bellows for the food industry, advancements in material science are enhancing the performance of rubber bellows.
Key Material Innovations
Silicone rubber: Silicone rubber bellows are ideal for environments that require heat resistance, making them perfect for high-temperature industrial applications.
Food-grade rubber: With the increasing focus on safety and hygiene in food processing, food-grade rubber bellows are being developed to meet strict regulatory standards.
Flexible rubber bellows: These bellows offer greater adaptability for various applications, from machine components to piping systems.
The future of rubber bellows will likely see further innovations in materials that offer better performance, reliability, and environmental sustainability.
Trend 4: Precision Moulding for Enhanced Quality
Precision moulding techniques are transforming the way rubber bellows are produced. Manufacturers are increasingly adopting advanced moulding technologies that allow for greater accuracy and uniformity in their products.
Benefits of Precision Moulding
Consistency: Precision moulding ensures that each rubber bellow is produced to exact specifications, leading to uniformity across the entire product range.
Quality control: It helps reduce defects in the finished product, ensuring higher reliability and durability.
Design flexibility: Modern moulding techniques allow for complex designs and shapes that were previously difficult to achieve.
Conclusion: Adapting to the Future
The rubber bellow manufacturing industry is evolving rapidly, driven by the demand for customization, sustainability, and advanced material technologies. By focusing on these key trends, manufacturers can meet the changing needs of industries and provide products that are more reliable, efficient, and adaptable than ever before.
As industries continue to rely on rubber bellows for their essential functions, manufacturers must remain committed to innovation and quality. At Namrata Rubber Products, we are dedicated to staying ahead of these trends and providing our clients with the best solutions for their specific needs. Thank you for reading our blog and taking an interest in our products, for more click on this to check out our product brochure.
Comments